While 3D models are often used for clash detection throughout the industry, the model for One Dalton was used to closely study the constructability of a major component of a building and to identify other design flaws, taking virtual design and construction to another whole level.
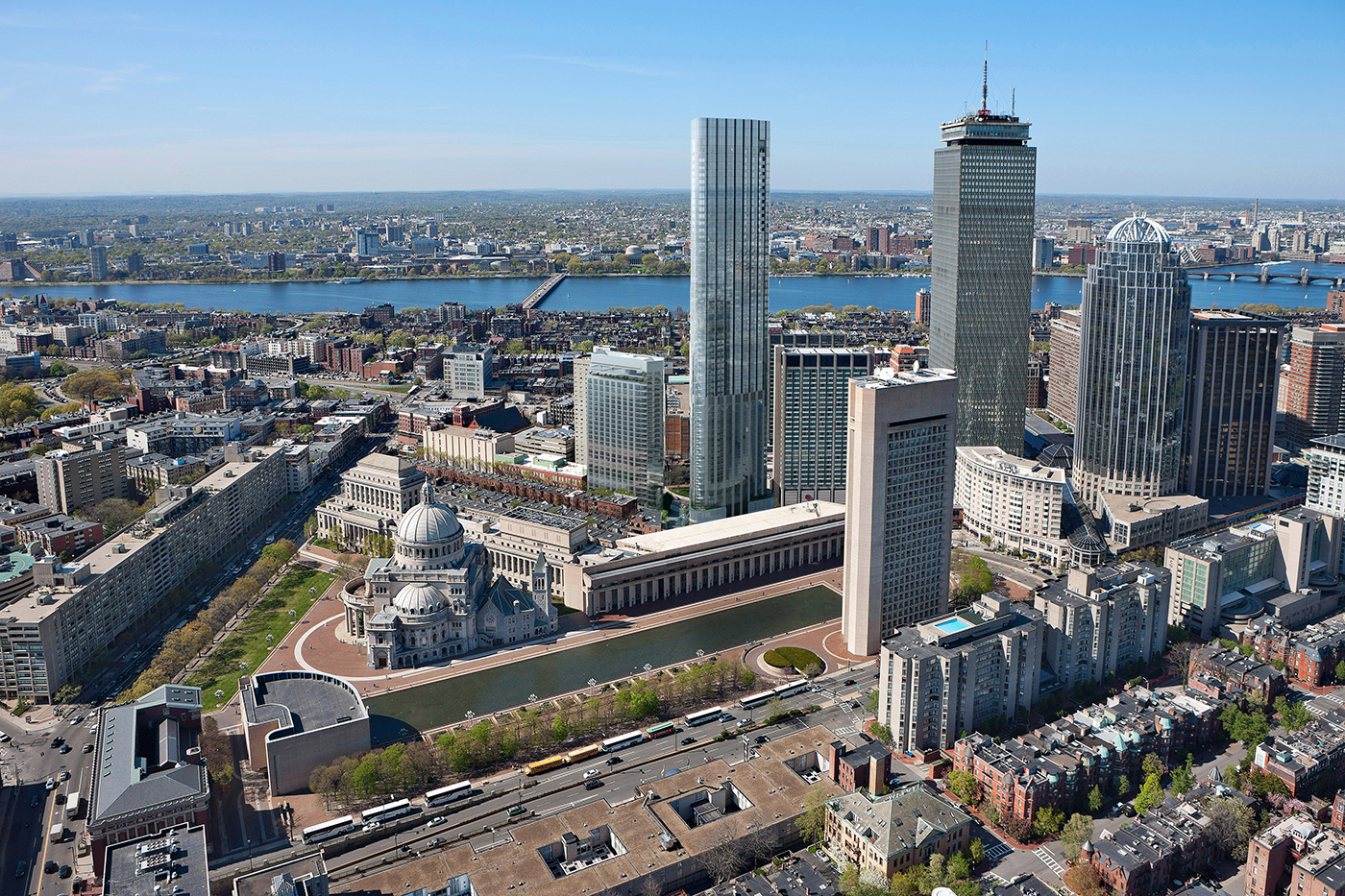
During the One Dalton project, the job of the belt truss, designed to span the 24th-26th floor, was to control excessive drift due to lateral load and help minimize the risk of structural damage due to wind or earthquakes. It was a critical component to the high-rise and was described as a “critical path” to completing the building on schedule.
Designed in 2D, the belt truss consisted of rebar (massive No. 20 bars) that was meshed too tightly together, which would not have allowed the concrete to flow in between the bars. The Suffolk team had an intuition that the belt truss could not be built the way it was designed, but they needed to prove their logic to the client and other partners.
The senior VDC manager on the project built a sophisticated and precise 3D virtual model of the belt truss and the rebar system from the original 2D design. Having a true and accurate visual representation of the design helped instill a trusting relationship between Suffolk and the design team. Together, Suffolk and the engineers collaborated and arrived at a solution.
The model proved that #20 rebar could not be bent/transitioned into other elements and that the design was too congested for concrete to flow. Discovering this issue later during the construction of the building would have led to significant delays and cost overruns — the project would have been completely stalled until new designs could be drawn up and approved. The 3D model was responsible for keeping the project on schedule.
The team’s discovery of the belt truss design challenges was critical to the project because this component of the building was considered a “show stopper”—ripping out rebar and concrete and then starting a new belt truss design from the beginning would have taken 10-12 months and would have cost millions of dollars in overages. At about $4,200 per square foot to purchase a condo and an average cost of $600 per guest room, the cost impact of that schedule delay from a client revenue standpoint would have been significant, especially when considering the number of units in the building (210 guest rooms and 185 luxury condos).
While 3D models are often used for clash detection throughout the industry, the model for One Dalton was used to closely study the constructability of a major component of a building and to identify other design flaws, taking virtual design and construction to another whole level.