Saving time and money with detailed drawings
By leveraging the detailed drawings and strategic planning elements inherent in Plan + Control, Suffolk reduced its general conditions by more than 10 percent and returned more than $2.5 million and three months in schedule to the team at 1700 Webster in Oakland.
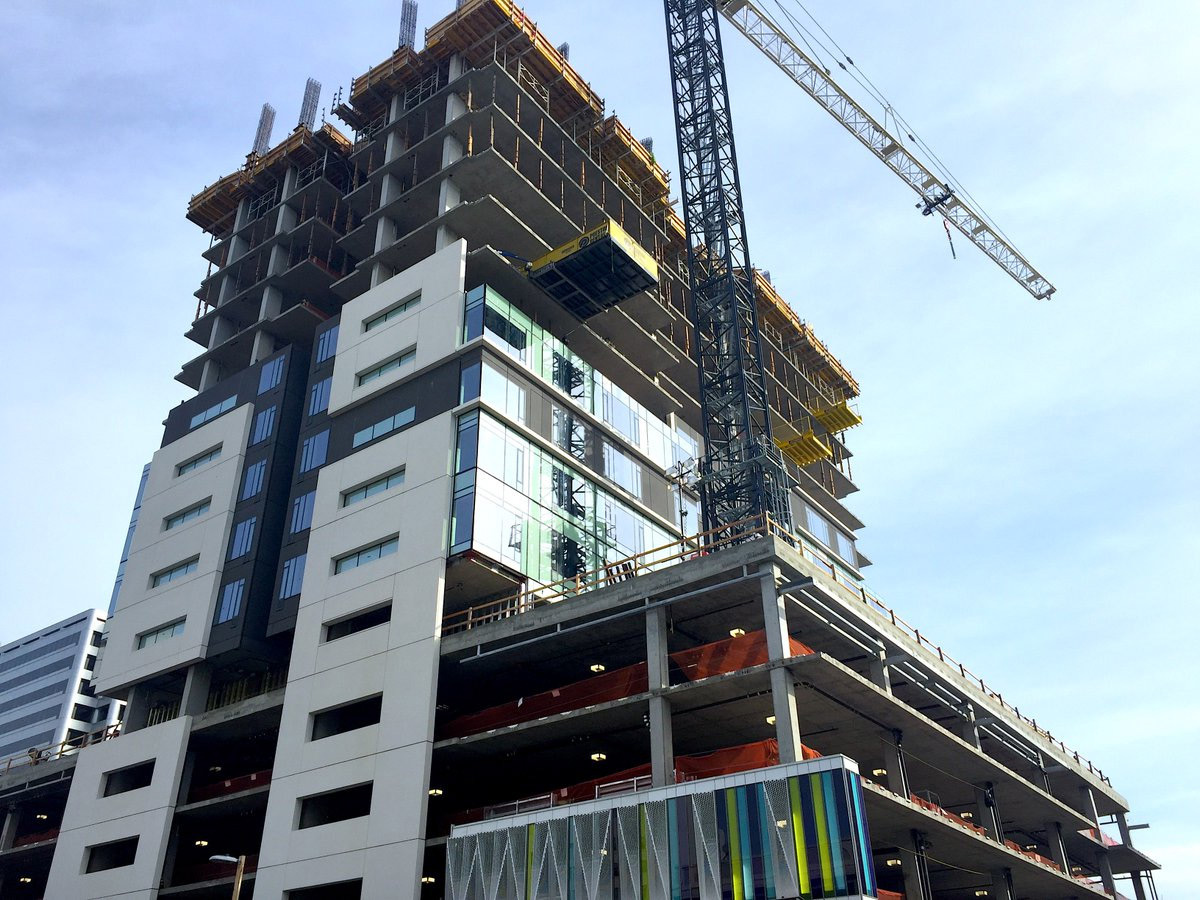
1700 Webster is the first high-rise building to break ground in Oakland since 2008. To seamlessly build the 24-story tower, Suffolk’s team performed extensive preconstruction services for the project, including a complete 5D estimating process, and followed the company’s innovative Plan+ Control process.
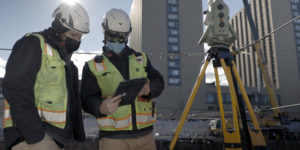
Plan + Control’s coordinated layout drawing step created detailed drawings that addressed any requests for information ahead of time. Every member of the construction team—design, contractor, trade partner—completed their own quality control and approved the drawings, creating accuracy and transparency. Suffolk superintendents and trade partners then had easy access to the drawings through Procore and iPad apps. These coordinated layout drawings drastically reduced the number of inquiries that trade partners had about constructability and geometry, resulting in only a dozen questions over the course of the two-year project.
In addition to the coordinated layout drawings, the team produced an entire set of backing drawings for the 206 apartment units and management drawings for concrete pours. With the backing drawings, all team members could look at each floor on their smartphones and understand how to correctly place the systems. Showing all the elements that were inside the walls made installation quick and easy: trade partners knew exactly where to mount electrical panels, then could roll into sheetrocking without having to worry about rework. For the concrete elements, the team was able to hand out information well in advance and fix any issues before the trucks were even scheduled. Because the 1700 Webster team resolved questions with Plan + Control ahead of time, they didn’t miss a pour date.
Because of the detail, accessibility, organization, and reliability of the drawings, subcontractors knew exactly what to build and when. This single point of truth led to major savings in both budget and time: Suffolk reduced its general conditions by about 10 percent, totaling $670,000, and was able to return more than $2.5 million to the client. The building earned its temporary certificate of occupancy three months ahead of schedule.